Accurate cost prediction, a cornerstone of effective project management, directly influences profitability. Poor cost management often leads to project overruns. Enhanced casting estimates, when applied strategically, are a crucial tool. Software solutions, such as Costimator, can streamline the estimation process. Successful implementation of enhanced casting estimates can result in substantial financial benefits, directly impacting an organization’s bottom line. The use of historical data helps refine cost estimates for future projects. In this article, we will examine how enhanced casting estimates can save you thousands.
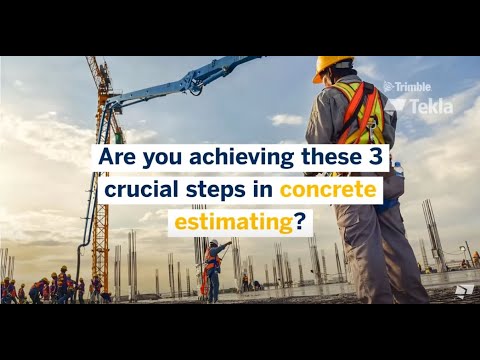
Image taken from the YouTube channel Tekla Software , from the video titled Better Performing Concrete Takeoffs – Estimator’s Guide to Modern Approach .
In the intricate world of manufacturing, casting stands as a cornerstone process, shaping raw materials into essential components. However, the path from molten metal to finished product is paved with complexities, and accurate cost estimation is paramount for project success. This is not merely an exercise in number-crunching; it’s the foundation upon which profitability, efficiency, and overall project viability are built.
The Indispensable Role of Precise Casting Estimates
Accurate casting estimates serve as a compass, guiding stakeholders through the financial landscape of a project. They provide a clear understanding of anticipated costs, allowing for informed decision-making at every stage, from initial design to final production. Without this clarity, projects risk veering off course, encountering unexpected expenses and potentially jeopardizing their financial health.
Consider the scenario of bidding for a large-scale casting project. An accurate estimate allows for competitive pricing while ensuring a healthy profit margin. It facilitates effective resource allocation, identifies potential bottlenecks, and ultimately contributes to project success.
The Price of Imprecision: Consequences of Inaccurate Estimates
Inaccurate casting estimates can trigger a cascade of negative consequences, rippling through the entire project lifecycle. Underestimation can lead to significant budget overruns, forcing difficult decisions such as compromising on material quality or delaying critical milestones. Overestimation, on the other hand, can result in lost bids and missed opportunities.
Beyond the immediate financial impact, inaccurate estimates can damage relationships with clients and suppliers, erode trust, and tarnish a company’s reputation. In today’s competitive landscape, where precision and efficiency are highly valued, the cost of inaccuracy is simply too high to bear.
Charting a Course for Cost Reduction: An Overview
The good news is that significant cost savings can be achieved through a combination of strategic planning, technological advancements, and a commitment to continuous improvement. This section offers a roadmap for navigating the complexities of casting cost estimation, highlighting key techniques and strategies for optimizing the entire process.
These include everything from carefully tracking fluctuating metal prices and optimizing labor costs to strategically selecting foundries and minimizing scrap rates. By embracing a data-driven approach and fostering a culture of cost consciousness, businesses can unlock substantial savings and gain a competitive edge in the marketplace. This involves implementing practical cost-effective strategies that will ultimately improve the bottom line.
The cost of inaccuracy, as we’ve seen, can be steep. To avoid these pitfalls, it’s essential to have a firm grasp on the individual components that make up a casting estimate. By meticulously examining each element, from material costs to scrap rates, businesses can identify opportunities for optimization and, ultimately, drive down expenses.
Understanding the Core Components of a Casting Estimate
Crafting an accurate casting estimate is not about guesswork; it’s about dissecting the entire process into manageable components. This involves a detailed evaluation of material costs, labor expenses, foundry selection, and, crucially, scrap rates. Each element presents unique challenges and opportunities for cost optimization.
Material Costs (Metal Prices)
Material costs, primarily driven by metal prices, often constitute a significant portion of the overall casting estimate. Managing these costs requires a multi-faceted approach, beginning with staying informed.
The Volatility of Metal Markets
Metal markets are dynamic and susceptible to fluctuations based on global supply and demand, geopolitical events, and economic indicators. Tracking these fluctuations is crucial for making informed purchasing decisions. Subscribing to industry reports, monitoring commodity exchanges, and utilizing specialized software can provide valuable insights into metal price trends.
Strategic Negotiation with Suppliers
Securing favorable pricing from suppliers requires proactive negotiation. This involves building strong relationships, exploring volume discounts, and considering long-term contracts to lock in stable prices. Don’t hesitate to obtain quotes from multiple suppliers to foster competition and ensure you’re receiving the best possible rates.
Minimizing Material Waste
Optimizing material usage during the casting process is paramount for cost reduction. Implementing techniques such as design optimization, efficient gating systems, and precise pouring practices can significantly minimize waste. Regular audits of the casting process can help identify areas where material losses can be reduced.
Labor Costs
Labor costs encompass both direct and indirect labor involved in the casting process. Understanding the breakdown of these costs is critical for identifying areas where efficiency can be improved.
Direct vs. Indirect Labor
Direct labor refers to the wages paid to workers directly involved in the casting process, such as molders, pourers, and finishers. Indirect labor includes the salaries of supervisors, maintenance personnel, and quality control staff. Differentiating between these costs provides a clearer picture of labor allocation.
Optimizing Labor Efficiency
Optimizing labor efficiency on the shop floor involves streamlining workflows, implementing lean manufacturing principles, and providing adequate training to employees. Ergonomic workstation design and efficient material handling systems can also contribute to improved productivity and reduced labor costs.
The Impact of Automation
Automation can significantly impact labor costs in casting. While the initial investment in automation equipment may be substantial, the long-term benefits can include reduced labor requirements, increased production speed, and improved product quality. Consider automating repetitive tasks or processes that are prone to human error.
Foundry Selection
Choosing the right foundry is crucial for both cost and quality. Different foundries specialize in different casting processes, materials, and production volumes.
Matching Needs to Foundry Capabilities
Selecting a foundry that aligns with your specific casting needs is essential. Consider factors such as the size and complexity of the castings, the required production volume, and the desired material properties. A foundry specializing in your specific requirements can often provide more competitive pricing and higher quality castings.
Negotiating Cost-Effective Contracts
Negotiating favorable contracts with foundries is vital for cost control. This involves carefully reviewing the foundry’s pricing structure, payment terms, and quality control procedures. Building a strong, collaborative partnership with the foundry can lead to long-term cost savings and improved communication.
Scrap Rates
Scrap rates represent the percentage of castings that are rejected due to defects. High scrap rates can significantly inflate the overall cost of casting.
Identifying Root Causes of Scrap
Identifying the root causes of scrap is crucial for implementing effective reduction measures. This involves analyzing scrap data, conducting root cause analysis, and investigating process deviations. Common causes of scrap include improper mold design, inadequate pouring techniques, and material contamination.
Implementing Scrap Reduction Measures
Implementing effective scrap reduction measures can significantly improve the efficiency and profitability of the casting process. These measures may include improving mold design, optimizing pouring parameters, implementing stricter quality control procedures, and providing additional training to employees.
The Financial Impact of Rework
Reworking defective castings is often costly and time-consuming. In addition to the direct labor costs associated with rework, there are also indirect costs, such as lost production time and increased energy consumption. Reducing scrap rates minimizes the need for rework and improves overall profitability.
The cost of inaccuracy, as we’ve seen, can be steep. To avoid these pitfalls, it’s essential to have a firm grasp on the individual components that make up a casting estimate. By meticulously examining each element, from material costs to scrap rates, businesses can identify opportunities for optimization and, ultimately, drive down expenses.
It’s time to look at how technology can be a force multiplier, enhancing accuracy and efficiency in the casting process.
Leveraging Technology for Enhanced Accuracy and Efficiency
The modern foundry operates in an environment where precision and speed are paramount. Technology offers the tools to not only meet these demands but also to exceed them, driving down costs and improving the overall quality of the final product.
Casting design and simulation software are at the forefront of this technological revolution, offering unprecedented capabilities for optimizing designs and processes.
The Power of Casting Design Software
Casting design software has revolutionized the initial stages of the casting process. These sophisticated tools allow engineers to create and refine designs virtually, identifying potential issues and optimizing for cost-effectiveness long before any physical prototypes are produced.
Optimizing Designs for Cost-Effectiveness
Casting design software allows engineers to explore various design options and assess their impact on material usage, manufacturing complexity, and overall cost.
By simulating the casting process, designers can identify areas where material can be reduced, or the design simplified, without compromising the structural integrity or functionality of the part. This proactive approach to design optimization can lead to significant cost savings, especially in high-volume production runs.
Early Identification of Potential Problems
One of the most significant benefits of casting design software is its ability to identify potential problems early in the design process.
Software tools use sophisticated algorithms to simulate the entire casting process, from mold filling to solidification, and can detect potential issues such as:
- Porosity.
- Hot spots.
- Distortion.
By identifying and addressing these problems virtually, engineers can avoid costly rework and delays later in the production cycle.
Process Optimization Through Simulation
Beyond design, technology plays a crucial role in optimizing the casting process itself. Casting simulation software allows foundries to model and analyze every aspect of the process, from metal flow to heat transfer.
This allows for fine-tuning parameters, optimizing cycle times, and minimizing defects.
Enhancing Process Optimization Efforts
Casting simulation provides valuable insights into how changes in process parameters, such as pouring temperature, mold design, or cooling rate, will affect the final product.
This allows foundries to experiment with different scenarios virtually, identifying the optimal combination of parameters for achieving the desired quality at the lowest possible cost.
Achieving the Best Balance of Cost and Quality
The ultimate goal of process optimization is to achieve the best possible balance between cost and quality.
By using casting simulation to fine-tune process parameters, foundries can minimize defects, reduce scrap rates, and improve the overall efficiency of the casting process. This leads to:
- Lower production costs.
- Faster turnaround times.
- Higher customer satisfaction.
In conclusion, leveraging technology through casting design and simulation software is no longer a luxury but a necessity for foundries seeking to remain competitive in today’s market. By embracing these tools, businesses can optimize designs, streamline processes, and drive down costs while maintaining the highest standards of quality.
It’s time to look at how technology can be a force multiplier, enhancing accuracy and efficiency in the casting process. But even the most advanced software is only as good as the people who wield it. The human element, particularly the expertise of cost estimators and project managers, remains indispensable in the pursuit of precise and cost-effective casting.
The Role of Skilled Professionals in Accurate Estimation
While technology provides invaluable tools, the experience and judgment of skilled professionals are critical for developing and managing accurate casting estimates. Cost estimators and project managers bring unique perspectives and capabilities that are essential for successful project execution and cost control.
The Indispensable Cost Estimator
The cost estimator stands as a cornerstone of the entire estimation process. They are responsible for meticulously analyzing all aspects of a casting project to determine its projected cost. Their expertise is crucial for setting realistic budgets, identifying potential cost overruns, and ensuring the financial viability of the project.
Key Skills and Qualifications
A competent casting estimator possesses a specific blend of skills and qualifications. They must have a thorough understanding of:
-
Casting Processes: A deep knowledge of various casting methods, their associated costs, and their suitability for different applications is fundamental.
-
Materials and Market Fluctuations: Staying abreast of metal market trends, understanding material properties, and sourcing materials at competitive prices are crucial.
-
Manufacturing Costs: Accurately calculating labor costs, overhead expenses, and other manufacturing-related costs is essential for a reliable estimate.
-
Data Analysis: The ability to analyze historical data, identify trends, and use statistical methods to predict future costs is highly valuable.
-
Communication Skills: Clearly and concisely communicating cost estimates to stakeholders, including engineers, project managers, and clients, is paramount.
The Project Manager’s Contribution
Project managers also play a critical, albeit often overlooked, role in accurate estimation and cost control. Their comprehensive understanding of the entire casting process, from design to final production, enables them to identify potential cost drivers and proactively manage risks.
Understanding the Process for Cost Control
A project manager’s understanding of the casting process informs accurate estimates and cost control in the following ways:
-
Process Optimization: Project managers can identify opportunities to streamline the casting process, reduce cycle times, and minimize waste, all of which contribute to lower costs.
-
Risk Management: By anticipating potential problems, such as material delays or equipment malfunctions, project managers can develop mitigation strategies to prevent cost overruns.
-
Communication and Collaboration: Project managers facilitate communication and collaboration among all stakeholders, ensuring that everyone is aligned on project goals and cost targets.
-
Performance Monitoring: Regularly tracking project progress against the budget and identifying any deviations allows for timely corrective actions to prevent costs from spiraling out of control.
It’s time to look at how technology can be a force multiplier, enhancing accuracy and efficiency in the casting process. But even the most advanced software is only as good as the people who wield it. The human element, particularly the expertise of cost estimators and project managers, remains indispensable in the pursuit of precise and cost-effective casting. Now, let’s shift our focus to a structured methodology for uncovering hidden value and driving down costs: value engineering.
Value Engineering: A Systematic Approach to Cost Reduction
Value engineering (VE) represents a structured, proactive approach to optimizing the value of a component, product, or process. In the context of casting, VE is not merely about cutting costs. It’s about meticulously examining every aspect of the casting – its design, materials, manufacturing process, and intended function – to identify and eliminate anything that doesn’t contribute to its essential purpose or performance.
Ultimately, VE is about achieving the best possible function at the lowest possible cost, without sacrificing quality, reliability, or customer satisfaction.
Unveiling the Essence of Value Engineering
At its core, value engineering is a systematic method to improve the "value" of goods or products and services by using an examination of function. Value, in this context, is defined as the ratio of function to cost. Value can therefore be increased by either improving the function or decreasing the cost.
Identifying and Eliminating Unnecessary Costs in Casting
The VE process in casting typically involves a multidisciplinary team that methodically analyzes the casting, breaking it down into its constituent parts and functions. The goal is to challenge assumptions, explore alternative materials and manufacturing methods, and identify areas where costs can be reduced or eliminated without compromising the casting’s performance.
This process often begins with a thorough functional analysis, asking key questions like:
- What is the purpose of this casting?
- What functions does it perform?
- Are there alternative ways to achieve these functions?
- What is the cost of each function?
- Are there any redundant or unnecessary functions?
Once the functions are clearly defined and understood, the team brainstorms alternative ways to achieve those functions, considering different materials, designs, and manufacturing processes.
Implementing Value Engineering in Casting: Real-World Examples
Consider a scenario where a complex casting requires extensive machining to meet tight tolerances. A value engineering approach might explore alternative casting methods, such as investment casting or precision sand casting, which can produce parts with closer tolerances, thereby reducing the need for costly machining operations.
Another example could involve a casting made from a high-cost alloy. Value engineering might investigate the possibility of using a less expensive alloy without compromising the casting’s structural integrity or performance. This could involve careful analysis of the application’s requirements and testing of alternative materials.
Furthermore, optimizing the casting design itself can yield significant cost savings. By simplifying the design, reducing the number of features, or optimizing the geometry for ease of manufacturing, it’s often possible to reduce material usage, cycle times, and scrap rates.
VE is not a one-time fix but an ongoing process. It requires a commitment to continuous improvement, a willingness to challenge assumptions, and a collaborative approach involving all stakeholders in the casting process.
Value engineering digs deep into why a casting costs what it does, but now it’s time to move from analysis to action. We’ll explore specific, actionable strategies for implementing cost-effective measures in your casting operations. These are the nuts and bolts of turning potential savings into real-world results.
Implementing Practical Cost-Effective Strategies
Translating value engineering insights into tangible cost reductions requires a multi-faceted approach. Standardization, material optimization, and yield improvement are key pillars of this strategy. Each area presents unique opportunities to streamline operations and drive down expenses.
The Power of Standardization in Casting
Standardizing casting processes offers numerous advantages, from reduced variability to improved predictability.
This means developing consistent procedures for everything from mold preparation to pouring techniques to post-casting finishing.
Streamlining for Efficiency
Standardization reduces the learning curve for new employees. It simplifies training and ensures consistent execution, regardless of the operator.
It also leads to fewer errors, less rework, and a more predictable output, ultimately lowering costs.
Furthermore, standardized processes are easier to monitor and optimize. You can identify bottlenecks and inefficiencies more readily when the process is consistent across all operations.
Documentation is Key
Clear, concise documentation is essential for successful standardization. This includes detailed work instructions, visual aids, and training materials.
The goal is to provide operators with everything they need to perform their tasks correctly and consistently. Regular audits and feedback sessions can help reinforce standardized practices and identify areas for improvement.
Material Optimization: Choosing Wisely
Selecting the right materials is critical for both performance and cost. Consider the application’s requirements and explore alternative materials that offer a better balance of cost and properties.
Beyond the Obvious Choice
Often, a slightly less expensive material can perform adequately without sacrificing critical functionality.
For example, in some applications, a lower grade of steel may be suitable, offering significant cost savings without compromising structural integrity.
Considering Total Cost of Ownership
Don’t just focus on the initial material cost. Consider the total cost of ownership, including factors like machinability, weldability, and corrosion resistance.
A material that is slightly more expensive upfront may be cheaper in the long run if it reduces machining time or extends the lifespan of the casting.
Maximizing Yield: Reducing Waste, Boosting Profits
Improving yield rates is a direct path to cost reduction. Reducing scrap and rework minimizes material waste, labor costs, and energy consumption.
Identifying Root Causes
Start by identifying the root causes of scrap. Common culprits include:
- Poor mold design
- Inadequate pouring techniques
- Improper cooling rates
Implementing Corrective Actions
Once you’ve identified the causes, implement corrective actions. This might involve redesigning molds, adjusting pouring parameters, or modifying cooling procedures.
Statistical process control (SPC) can be a valuable tool for monitoring yield rates and identifying trends.
By tracking key metrics and implementing process improvements, you can continuously reduce scrap and improve yield.
Unleashing the Benefits of Process Optimization
The benefits of process optimization extend far beyond just cost reduction. Optimized casting processes often lead to:
- Improved quality
- Shorter lead times
- Increased capacity
By continuously refining your processes, you can achieve significant improvements in all areas of your casting operation.
Data-Driven Decisions
Process optimization should be data-driven. Collect data on all aspects of the casting process. Analyze it to identify areas for improvement.
Simulation software can be invaluable for optimizing casting processes.
It allows you to model different scenarios and predict the impact of changes before implementing them in the real world. This minimizes the risk of costly mistakes and accelerates the optimization process.
FAQs: Enhanced Casting Estimates & Savings
[This section answers common questions about enhancing your casting estimates to save money. We’ve compiled these based on feedback and inquiries.]
What exactly are "enhanced casting estimates"?
Enhanced casting estimates involve a more detailed and accurate breakdown of all costs associated with your casting project. This includes material costs, labor, machining, finishing, and any potential hidden fees. They aim to provide a clearer picture than standard, less comprehensive estimates.
How can enhanced casting estimates actually save me money?
By identifying potential cost overruns early on, enhanced casting estimates allow you to make informed decisions. You can negotiate better pricing, optimize designs for material efficiency, and avoid costly surprises during production. The transparency provided leads to smarter spending.
What key elements should I look for in an enhanced casting estimate?
Look for a detailed breakdown of material costs, including alloy type and quantity. The estimate should also itemize labor costs for each stage of the process, from mold creation to finishing. Clear communication about potential risks and contingency plans is also crucial.
Are enhanced casting estimates difficult to obtain?
While they may require more initial effort to prepare, many reputable casting foundries offer enhanced casting estimates. Be upfront about your needs and request a detailed breakdown. The upfront investment of time is worth it in the long run to prevent budget overruns.
So there you have it – a few tips to supercharge your enhanced casting estimates! Hopefully, this has given you some food for thought and inspires you to refine your approach. Happy casting!